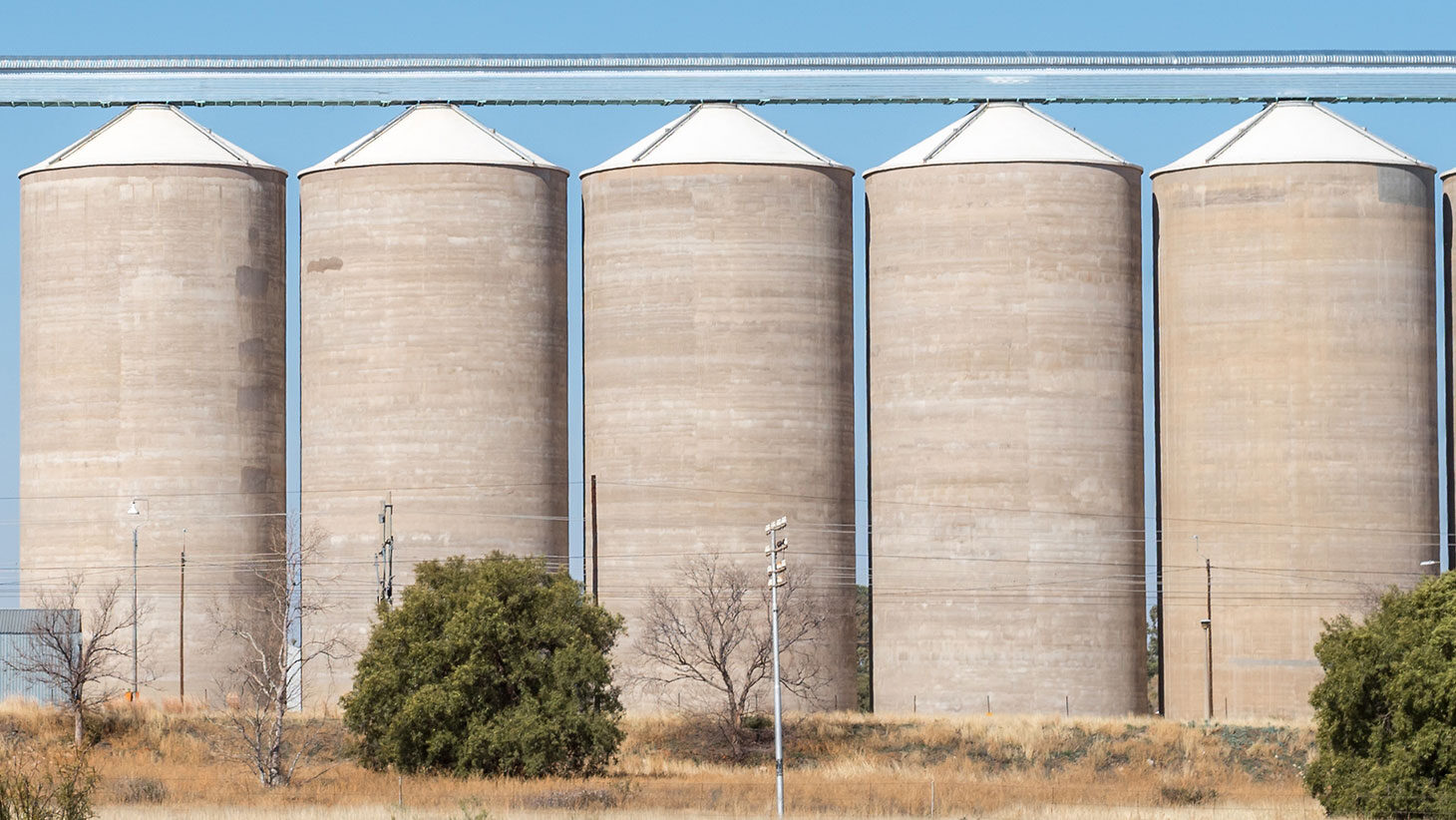
Pubblicato da ESSS Italia,
Modellazione dei silos per lo stoccaggio della soia
Nell'agricoltura, i silos sono unità destinate allo stoccaggio dei prodotti. E molti dei silos esistenti nel mondo non presentano condizioni operative ideali a causa della mancanza di conoscenza della distribuzione della pressione, del flusso e del gran numero di variabili che influenzano il comportamento dei prodotti stoccati. Questo spiega anche il numero significativo di incidenti e crolli in queste strutture. Per questo motivo, la modellazione dei silos computerizzata sta diventando sempre più importante per l'industria agroindustriale.
In questo post presenteremo lo studio accademico condotto dal professor Fábio Selleio Prado e dai suoi studenti André Candido de Vasconcelos, Bruno Toledo de Vasconcelos e Kaique Chammas Uzan del Centro Universitario dell'Istituto di Tecnologia di Mauá in Brasile.
L'obiettivo principale è analizzare la distribuzione delle pressioni che i semi di soia stoccati possono esercitare sulle pareti della struttura dei silos bassi con scarico eccentrico, verificando l'aderenza dei risultati numerici ottenuti alla norma europea EN-1991-4-2006.
A tale scopo sono stati utilizzati strumenti informatici come Ansys Rocky e Ansys Mechanical e i risultati sono stati presentati al X Congresso brasiliano di ponti e strutture a Rio de Janeiro, in Brasile.
Panoramica attuale dei modelli di stoccaggio dei cereali
Il Brasile ha registrato un continuo aumento della produzione e delle scorte di cereali. Tuttavia, a partire dagli anni 2000, la capacità di stoccaggio statico non è più riuscita a tenere il passo dell'aumento della produzione, lasciando un deficit di stoccaggio nelle scorte brasiliane.
In generale, secondo Carlito Calil Junior, professore del Dipartimento di Ingegneria Strutturale dell'USP, i silos utilizzati per lo stoccaggio nelle aziende agricole hanno un basso rapporto tra l'altezza e il diametro o lato, e il fondo piatto. Ciò è giustificato dal fatto che la capacità del silo aumenta con l'aumentare del suo diametro, e anche perché la movimentazione dei sili bassi è più facile e meno costosa.
Per questo motivo, la modellazione dei silo è importante per studiare il comportamento strutturale dei silo con un basso rapporto altezza/diametro realizzati in calcestruzzo, poiché si tratta di un sistema ampiamente utilizzato per lo stoccaggio di questi elementi grazie alla sua enorme versatilità, in quanto può essere modellato in loco, prefabbricato, rinforzato convenzionalmente o precompresso e a forma di cupola.
Tuttavia, l'analisi strutturale non è semplice da eseguire, in quanto sono coinvolti diversi tipi di carichi sulla struttura (vento, scarico e carico dei grani), diverse modalità di scarico del silo (che generano diverse combinazioni di sforzi) e molti tipi di materiali di stoccaggio con le più svariate proprietà fisiche, quali: granulometria, peso specifico, angolo di attrito interno, angolo di attrito effettivo e angolo di attrito con la parete, oltre al fatto che i grani hanno una forma granulare o polverosa, un fatto che altera notevolmente i criteri di calcolo strutturale.
L'analisi computazionale è quindi necessaria per valutare come si distribuiscono le forze in questo tipo di struttura.
Guarda il webinar: https://www.esss.com/it/contenuti/workshop-efficienza-nella-simulazione-di-particelle-con-ansys-rocky/
Metodologia utilizzata nello studio
Per effettuare i confronti desiderati, è stato utilizzato un progetto di silo esistente come base per gli studi iniziali, effettuando adattamenti alle esigenze dell'analisi e ai limiti di calcolo. Questa struttura è stata progettata con Ansys SpaceClaim, analizzata con Ansys Mechanical e la simulazione del movimento dei grani è stata riprodotta fedelmente in Rocky DEM.
Per analizzare la distribuzione delle pressioni per questo tipo di struttura, il caso di studio è iniziato con la progettazione di un silo di grandi dimensioni con un diametro e un'altezza delle pareti di 90 m e 45 m rispettivamente.
Modellazione dei sili: determinazione delle pressioni verticali sulle pareti
Per valutare gli effetti dello scarico, il silo deve essere prima riempito fino all'altezza della parete, e per questo si è calcolata una portata di 110.000 tonnellate/h per un tempo di riempimento di 10 secondi. Il silo è stato riempito attraverso l'ingresso sopra la cupola, come mostrato nella Figura 1 qui sotto:
Figura 1- Riempimento del silo attraverso la cupola
Modellazione di silos: determinazione delle sollecitazioni principali nella parete verticale
In una prima analisi, le sollecitazioni sono state valutate ogni 4 secondi di scarico. È servito a valutare il momento in cui si verifica la pressione massima, per poi ridurre il passo temporale al fine di trovare l'istante più vicino alla sollecitazione massima.<
Risultati
Con elementi rettangolari di 0,25 m di altezza ciascuno, le pressioni sono state determinate partendo dalla coordinata 3,875 m (4,00 m - 0,25/2 m), che rappresenta il centro geometrico del primo elemento che riceve la pressione visto dall'alto, e determinando i rispettivi valori camminando con un passo di 0,25 m fino a raggiungere il centro dell'elemento più basso nella parete verticale del silo con zSAP = 0,125 m.
Pressioni verticali della parete
Rocky, che è stato utilizzato nella seconda analisi per ottenere i valori di pressione, fin qui calcolati utilizzando le linee guida della norma europea, fornisce i valori del modulo delle pressioni quando vengono esportati, quindi a scopo di confronto è stato calcolato il modulo tra le pressioni orizzontali (ph) e tangenziali (pw) per i 3 canali di flusso.
Le figure 2, 3 e 4 mostrano i valori delle pressioni commentate e calcolate per i tre canali di flusso proposti dalle linee guida di calcolo della norma EN-1991-4-2006, dove PRce si riferisce alle pressioni all'uscita del canale di flusso, PRae alle pressioni nelle zone adiacenti all'uscita del canale e PRse indica le pressioni che si verificano lontano dall'uscita del canale di flusso.
Figura 2: Confronto delle pressioni all'uscita dei 3 canali di flusso proposti dalla norma EN-1991-4-2006. Figura 3: Confronto delle pressioni adiacenti dei 3 canali di flusso proposti dalla norma EN-1991-4-2006.
Figura 4: Pressioni costanti proposte dalla norma EN-1991-4-2006.
Sollecitazioni principali nella parete verticale - Ansys Rocky
Quando si eseguono analisi con il software Ansys, le pressioni e le sollecitazioni possono essere valutate per ogni passo temporale. Ciò rende difficile ottenere i valori ideali da confrontare con i risultati ottenuti dalla norma EN-1991-4-2006.
Pertanto, per ottenere questi valori, lo studio è stato effettuato prima con le tensioni, ottenendo i risultati massimi per intervalli di tempo variabili ogni 4 secondi. Questo mostra che la tensione principale massima si verifica in un momento vicino ai 18 secondi.
Su questa base, è interessante valutare le sollecitazioni in passi temporali più piccoli per ottenere un'analisi più raffinata in prossimità dell'istante di 18 secondi. Pertanto, è stato adottato un passo temporale di 1 secondo, valutando i risultati fino a ottenere il picco di tensione, che dovrebbe essere intorno all'istante 18s. Di conseguenza, si è notato che l'istante di 17s (7 secondi di scarico) è stato il momento in cui si è ottenuta la massima sollecitazione principale nella struttura.
Dopo questo momento, le tensioni iniziano a diminuire. La Figura 5 mostra come le sollecitazioni ottenute seguano il modello di distribuzione della pressione lungo la parete proposto dalla norma europea EN-1991-4-2006.
Figura 5: le sollecitazioni ottenute seguono l'andamento della distribuzione della pressione.
La Tabella 1 e la Figura 6 mostrano come le tensioni variano nel tempo, con un maggior numero di istanti analizzati in prossimità dell'istante 18s, al fine di ottenere il momento in cui si verifica il picco di tensione.
Figura 6 - Grafico che mostra la variazione della sollecitazione principale massima nel tempo.
Pertanto, una sollecitazione principale massima di 459,1 kPa è stata ottenuta a un tempo di 17 secondi (5 secondi dopo l'inizio dello scarico).
Confronto tra le analisi
In primo luogo, è possibile confrontare le pressioni e le sollecitazioni generate per i 3 canali di flusso proposti dalla norma europea EN-1991-4-2006.
Si può notare che le pressioni risultanti all'uscita del canale di flusso sono più alte nel caso 3 e più basse nel caso 1, con i valori del caso 2 che sono intermedi, secondo la Figura 2.
D'altra parte, l'analisi della Figura 3 mostra un'inversione, in quanto le pressioni nella zona adiacente del caso 1 sono più elevate di quelle del caso 3, per lo stesso motivo.
Conclusioni
Le pressioni sono state ottenute in modo diverso per le due analisi. Nella prima, sono state realizzate 3 alternative per la geometria del canale di scorrimento proposte dalla norma europea EN-1991-4-2006 attraverso il calcolo manuale, tenendo conto della possibilità di variare le caratteristiche del canale, che devono variare non solo con le caratteristiche dei grani, ma anche con le caratteristiche ambientali e istantanee.
Ne risultano valori di modulo diversi per le pressioni orizzontali e tangenziali in ciascun caso, con distribuzioni leggermente diverse a seconda della geometria stimata per ciascun canale di flusso.
Tuttavia, confrontando le pressioni ottenute direttamente dall'interazione dei grani con la struttura utilizzando il software Rocky, si può notare che i risultati ottenuti dalla norma europea sono soddisfacenti e, di fatto, cercano di soddisfare i requisiti di progettazione se confrontati con l'analisi raffinata.
Nonostante ciò, con lo studio effettuato da Rocky interagendo con altri software Ansys, si sono ottenuti risultati soddisfacenti per quanto riguarda la distribuzione delle pressioni e l'analisi dinamica studiata in modo semplificato con diversi studi in un tempo lungo.
Con l'interazione automatica tra i grani e la struttura, a provocare le variazioni di carico proposte, si può confermare che il comportamento delle particelle durante lo scarico è vicino al comportamento atteso proposto dalla norma. È importante affinare un'analisi di questo tipo, nella quale le pressioni che i grani esercitano sulla struttura sono state spesso trattate come se fossero liquidi, causando molte catastrofi in passato, che spesso si sono protratte fino ai giorni nostri.
L'utilizzo del software Ansys, e Rocky, per la modellazione dei silo non è solo una questione di economia e sicurezza, ma anche di previsione, e con la garanzia di star utilizzando quanto di meglio dimostratosi in fatto di simulazione di particelle.
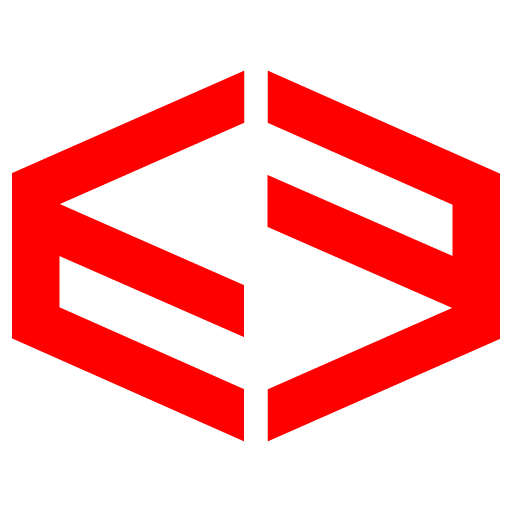
ESSS Italia
ESSS Italia è un Ansys Apex Channel Partner e azienda leader nel settore del software di ingegneria. Offre supporto e servizi di alto livello che aiutano ingegneri e progettisti a prendere decisioni ottimali nelle diverse fasi del ciclo di vita di un prodotto o processo, inclusi progettazione, selezione dei materiali, costruzione, risoluzione di problemi e manutenzione.
TAGS:
#Simulazione strutturale