Una pompa, o macchina operatrice, è una macchina fluidodinamica che sfrutta il movimento di organi meccanici per sollevare o movimentare fluidi. In questo articolo vedremo quali sono le caratteristiche principali, come vengono classificate, quali sono le principali applicazioni; inoltre verrà fatto cenno sulle principali normative che guidano la loro progettazione. Scopriremo, infine, quali sono le sfide per gli ingegneri di oggi e come l’impiego di simulazioni numeriche CFD può essere la carta vincente per migliorare e ottimizzare il funzionamento di una pompa.
Quali sono le caratteristiche principali di una pompa?
Per distinguere una pompa rispetto ad un’altra, i tecnici spesso tengono conto di caratteristiche come:
- Portata: è un indice di quanto fluido può spostare o movimentare nel tempo una macchina operatrice;
- Prevalenza: indica qual’è il salto superabile, in altezza, dalla pompa;
- NPSH: dall’inglese Net Positive Suction Head, letteralmente prevalenza netta di aspirazione positiva, indica la pressione assoluta che deve esistere sull’aspirazione della pompa affinché non insorgano fenomeni problematici come la cavitazione.
Spesso nella scelta di una macchina operatrice si tiene conto anche delle caratteristiche del fluido come la viscosità, la densità e la temperatura. Questi parametri infatti possono essere molto influenti e determinanti per effettuare un’ottima scelta.
Come vengono classificate le macchine operatrici?
Le pompe possono essere classificate in:
- Volumetriche: la movimentazione del liquido avviene per mezzo della variazione di volume. Sono caratterizzate da una portata costante per ogn
i ciclo di funzionamento. Le pompe volumetriche, sfruttano vari meccanismi per far variare il volume della camera di pompaggio, infatti esistono pompe ad ingranaggi, a lobi, a palette, a vite, a pistoni, ecc. Di conseguenza si possono avere pompe volumetriche alternative o rotative.
- Fluidodinamiche: funzionano per mezzo della dinamicità del fluido stesso per imprimere la forza di pompaggio necessaria. Questa tipologia di macchina a differenza di quella volumetrica non ha bisogno di valvole. Ma a loro discapito hanno che all’aumentare della pressione richiesta in uscita, diminuisce la portata possibile. Di conseguenza anche la loro efficienza ne risente. Inoltre per il loro funzionamento, a volte, richiedono alcune condizioni di partenza come l’adescamento, cioè c’è bisogno che la pompa si riempia di fluido prima dell’accensione. Anche questa tipologia di pompe sfrutta vari principi di funzionamento, si possono trovare infatti pompe fluidodinamiche centrifughe, lineari, magnetiche e assiali.
Inoltre a seconda della portata, si possono classificare pompe a portata costante e a portata variabile. Altra classificazione importante sta nel modo di installazione delle macchine operatrici. Queste infatti possono essere:
- Di superficie: sono pompe disposte al di fuori del fluido di pompaggio e solitamente utilizzano un tubo di pescaggio;
- Ad immersione: sono immerse nel fluido da movimentare;
- Integrate: queste varianti di macchine non funzionano autonomamente, ma fanno parte di un complessivo di elementi a cui sono accoppiate;
- Di spurgo: si possono considerare degli ibridi, in quanto sono il giusto compromesso tra le pompe di superficie e quelle ad immersione. Infatti per il loro funzionamento, non devono essere raffreddate sfruttando per forza di cose l’immersione totale nel fluido. Di contro, queste pompe non operano su grandi prevalenze
Dove e per cosa vengono utilizzate le pompe?
Le macchine operatrici trovano un largo impiego in svariati settori, ma tra quelli principali ci sono la depurazione e il trattamento delle acque, gli impianti industriali, specialmente chimici e farmaceutici, impianti di smaltimento rifiuti urbani, piscine, impianti pubblici, parchi acquatici, impianti termali, trattamenti superficiali dei materiali, trattamento dell’aria e condizionamento (sistemi HVAC), raffinerie e attività minerarie, la produzione di energia e centrali elettriche, la cantieristica navale e piattaforme offshore, industria tessile e conciaria e infine nella fertirrigazione e nelle serre.
Quali sono le principali normative per le macchine operatrici?
Tra le principali normative, che è possibile prendere in considerazione quando si vuole progettare e/o collaudare una pompa ci sono le seguenti, divise per tipologia:
Pompe volumetriche
Le normative API (American Petroleum Institute), di derivazione americana, sono tra le principali normative di riferimento:
API 676 è la normativa che si applica alle pompe volumetriche rotative.
API 675 è la normativa applicabile alle pompe dosatrici alternative, con sistema di regolazione della corsa e in grado di fornire una portata precisa e ripetibile nel campo 10-100%.
API 674 è la normativa applicabile alle pompe alternative a corsa fissa.
Pompe fluidodinamiche
Accostate a queste, trovano anche spazio le normative ISO e UNI:
ISO 2858-1975 che si riferisce alle pompe centrifughe di uso generale e di processo, con flange metriche;
API 610 che si riferisce a pompe di processo, con flange in unità imperiali, fluidodinamiche;
UNI 9584 Pompe centrifughe, ad uno stadio con aspirazione assiale per acqua, PN 10 requisiti di sicurezza;
UNI EN 733 Pompe centrifughe, ad aspirazione assiale, pressione nominale 10 bar, con supporti. Punto di funzionamento nominale, dimensioni principali, sistema di designazione;
UNI EN 22858 Pompe centrifughe, ad aspirazione assiale, pressione nominale 16 bar, condizioni nominali di esercizio e dimensioni.
Ovviamente questa lista non può essere ritenuta esaustiva, in quanto ogni caso specifico potrebbe aver bisogno di essere adeguatamente valutato secondo ulteriori normative.
Quali sfide e problemi si presentano nella progettazione di una pompa?
La maggioranza delle sfide progettuali odierne che gli ingegneri devono affrontare sono imputabili al processo di progettazione di una pompa. Ma non sono da sottovalutare anche i vincoli dettati dalle condizioni d’esercizio. Spesso il processo di progettazione implica la costruzione di prototipi fisici, che contribuiscono in maniera preponderante ad aumentare i costi. Di conseguenza, anche i costi per il collaudo non sono trascurabili. Spesso questo approccio limita la valutazione solo a poche configurazioni, andando a trascurare numerosi altri design e si ha comunque una limitata conoscenza di ciò che accade internamente. I principali obiettivi per costruire una buona pompa sono, avere bassi consumi di potenza, alta efficienza e la maggiore prevalenza possibile.
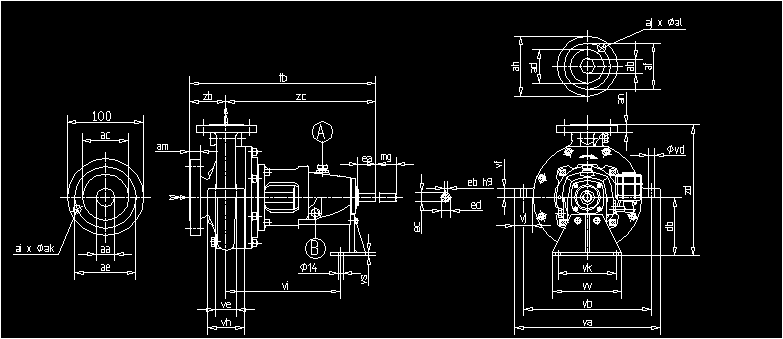
Uno dei principali problemi con cui spesso gli ingegneri e i tecnici devono confrontarsi è l’insorgenza della cavitazione. Questo succede quando la dinamica del flusso è tale da far scendere la pressione locale al di sotto della tensione di vapore, e comporta la comparsa di bolle di vapore all’interno del liquido. Le bolle di solito durano poco tempo e collassano quando incontrano una pressione maggiore.
La cavitazione può causare rumore e vibrazioni, usura strutturale e danni, e tutto questo va ad abbassare le prestazioni complessive. È un problema comune nelle pompe, che si presenta particolarmente in quelle volumetriche e centrifughe. Per questo la cosa migliore da fare è identificare il problema già all’inizio del processo di progettazione in maniera da ottenere un design efficace. Spesso però, l’approccio tradizionale e i test fisici non sono sufficienti ad identificare il problema, in quanto la cavitazione di solito compare solo quando si raggiungono elevati livelli di vibrazione e rumorosità. Inoltre, anche dopo la rilevazione di tali rumorosità, è complicato appurare che la cavitazione ne sia la causa principale. Senza un’accurata previsione del problema, i produttori rischiano di esporre i loro prodotti a vibrazioni e danni imprevisti.
La simulazione CFD è la soluzione!
Per questo una delle principali soluzioni è la simulazione numerica. Simulare le problematiche che una pompa potrebbe presentare richiede conoscenze ingegneristiche avanzate. Ma praticamente è possibile modellare con precisione qualsiasi pompa. Per fare questo, la fluidodinamica computazionale applica diversi metodi, andando a distinguere diverse tecniche per le parti rotanti:
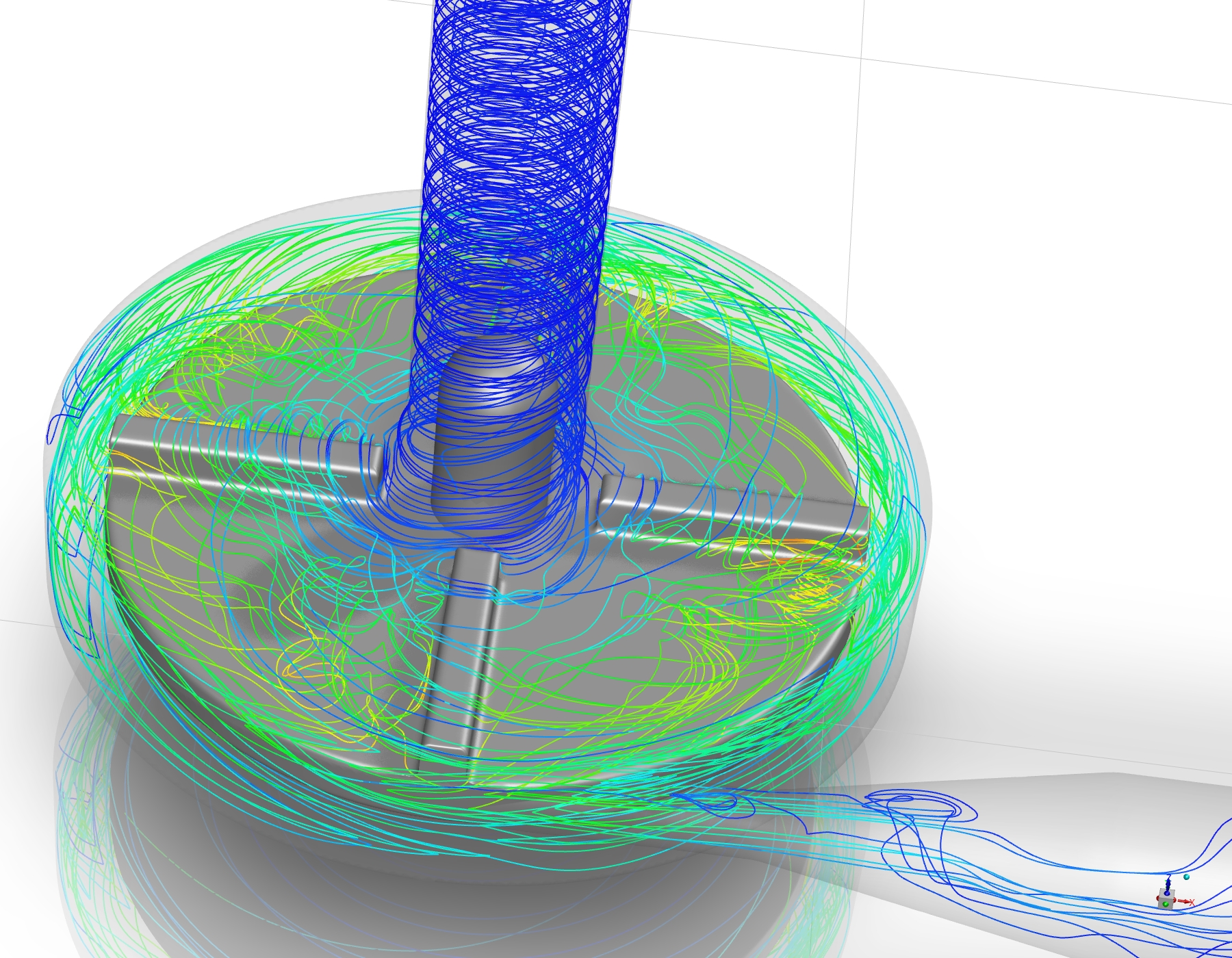
Il metodo SRF (dall’inglese Single Reference Frame), usa un solo sistema di coordinate, in cui l’intera soluzione è simulata in un sistema di riferimento rotante. Questa è la tecnica di modellazione numerica più semplice, basata sul concetto di moto relativo. In questo caso si usa un approccio stazionario e i componenti in movimento sono considerati stazionari nel sistema di riferimento rotante mentre i componenti fissi (come l’alloggiamento della pompa), ricevono una rotazione opposta rispetto al sistema di riferimento. Questo modello è utile quando si hanno pompe assialsimmetriche.
Il metodo MRF (dall’inglese Multiple Reference Frames), consente di utilizzare più sistemi di riferimento rotanti. Con questo approccio, viene analizzata solo una posizione della girante rispetto all’alloggiamento, quindi è meglio se il campo di flusso lungo l’interfaccia non sia fortemente dipendente dall’orientamento della girante. Sebbene l’analisi del campo di flusso sia allo stato stazionario, il metodo può essere utilizzato anche per analisi transitorie, che coinvolgono altre variabili del problema.
Il metodo mixing plane è una variante del modello MRF, in cui le variabili di flusso sono mediate circonferenzialmente all’interfaccia tra i domini. Questo approccio, viene spesso utilizzato per file di pale multiple in pompe multistadio, specialmente se le variazioni tra gli stadi sono piccole.
Il metodo sliding mesh, è un approccio transitorio che calcola il campo di moto quando una regione della mesh ruota rispetto ad un’altra. Mentre le due mesh scorrono l’una sull’altra, le informazioni vengono scambiate attraverso la loro interfaccia condivisa. Questo approccio rigoroso è utile per esaminare i transitori all’avviamento, e gli effetti turbolenti transitori, utilizzando anche modelli di turbolenza LES ( dall’inglese Large Eddy Simulation).È utile nel caso di una massiccia presenza di interazioni tra le componenti rotanti e fisse.
Il metodo dynamic mesh, minimizza la necessità di rigenerare la mesh tramite varie tecniche, aumentando l’accuratezza della previsione. I movimenti delle regioni di mesh bidimensionali e tridimensionali possono essere specificati dall’utente come spostamenti relativi rispetto alla mesh iniziale o rispetto a posizioni assolute. Il solutore successivamente determina lo spostamento dei nodi della griglia in tutto il dominio, intervenendo con tecniche di smoothing, layering e remeshing. La soluzione viene infine mappata sulla nuova mesh modificata.
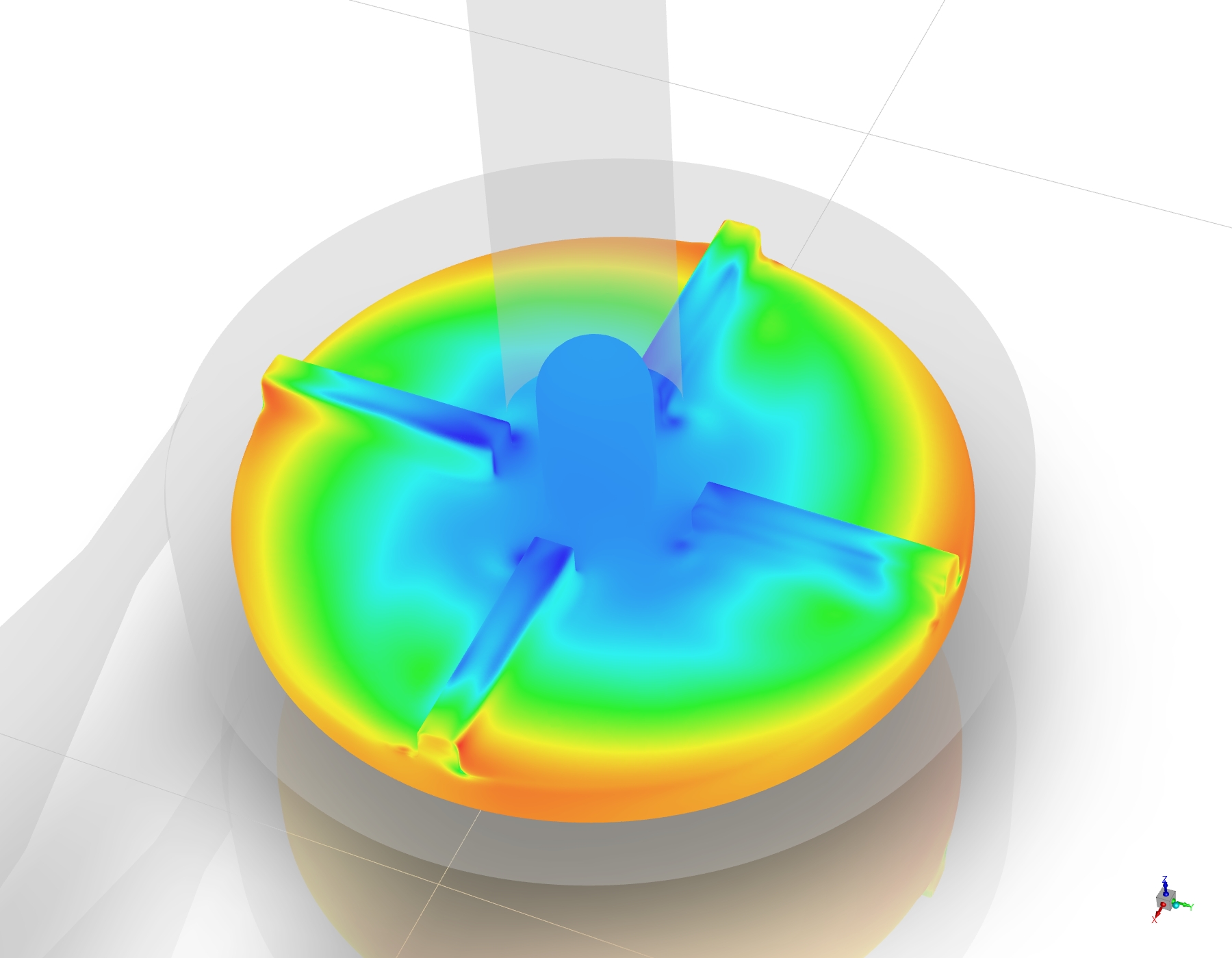
Un focus particolare invece è richiesto sulla cavitazione, infatti per gestire al meglio l’insorgenza di questo fenomeno gli ingegneri e i tecnici progettisti adottano solutori di analisi CFD che attualmente offrono un’ampia gamma di funzioni avanzate; tra queste esiste la possibilità di scegliere modelli e sottomodelli adatti ad interpretare e prevedere la cavitazione. Quelli più conosciuti sono:
Questi sottomodelli di cavitazione prendono in considerazione la crescita ed il collasso delle bolle di vapore, insieme al trasferimento di massa tra le fasi. Vengono quindi tracciate le interfacce che separano le regioni gassose da quelle liquide, tenendo conto delle grandi differenze di densità tra queste regioni, che causano sostanziali variazioni nel regime di flusso, nello scambio termico e di massa. Il set di equazioni differenziali a derivate parziali per modellare la termofluidodinamica deve essere separato e distinto per la fase liquida e la fase gassosa rispettivamente. Mentre lo scambio di massa, energia e quantità di moto tra le fasi viene introdotto con dei termini di trasferimento aggiuntivi inseriti nelle equazioni. I modelli di cavitazione possono essere applicati con qualsiasi modello di turbolenza, inclusi i modelli LES, che risolvono direttamente grandi vortici mentre modellano vortici più piccoli.
Quali sono i vantaggi delle simulazioni fluidodinamiche?
Grazie ai progressi dell’ingegneria, attualmente i software di fluidodinamica computazionale, hanno raggiunto una tale precisione che sono diventati strumenti essenziali per la progettazione e l’analisi di dispositivi come le pompe. Le simulazioni CFD correttamente utilizzate e convalidate, consentono agli ingegneri di andare oltre alle semplici linee guida dedotte dall’esperienza e dalle correlazioni empiriche e permettono di arrivare a predire in maniera approfondita ed esauriente le caratteristiche del flusso. L'analisi CFD è diventata indispensabile per fornire una visione dettagliata dei processi e degli organi delle pompe che prima venivano considerate a scatola chiusa.
Infatti, l’analisi fluidodinamica per mezzo di simulazioni numeriche può fornire informazioni utili, sia sulle prestazioni complessive della pompa, sia sui dettagli del flusso all’interno della pompa, tenendo conto anche delle perdite di flusso grazie all’impiego di appositi modelli numerici che si adattano ai vari livelli di prevalenza. Infine i risultati ottenuti dalle simulazioni CFD possono essere sfruttati nel processo di ottimizzazione del design della pompa.
Se vi interessa avere maggiori informazioni su questa metodologia e scoprire i vantaggi che la tua azienda avrebbe nell'integrarla all'interno dei suoi processi di progettazione e produzione contattaci, uno dei nostri esperti risponderà a tutte le tue domande.