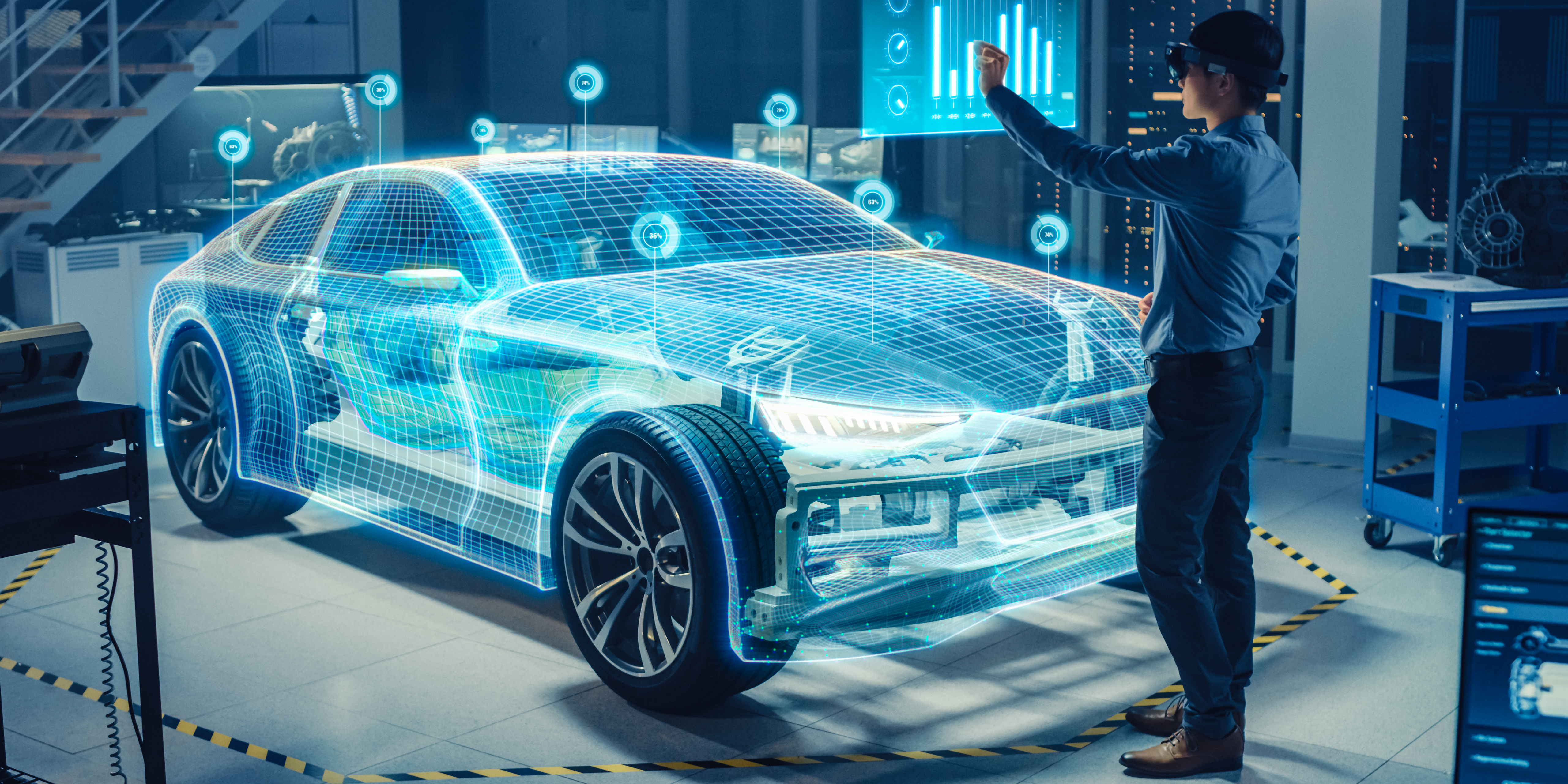
Interessante notare come l'aumento della complessità del prodotto venga al primo posto, seguita dalla necessità di ridurre il time to market, migliorando al contempo la qualità (che viene citata al terzo posto). Val la pena quindi approfondire come gli strumenti CAE (Computer Aided Design) vengano utilizzati a supporto di queste iniziative e per farlo faremo un breve excursus sul tema più generale della digitalizzazione.
La digitalizzazione
Oggi tutti parlano di digitalizzazione, anche i mass-media principali la citano spesso. Ma cosa significa digitalizzare e, soprattutto, a cosa serve?
La risposta banalmente è: trasferire le informazioni disponibili su documenti fisici, nella maggior parte cartacei, in un formato digitale memorizzato su un elaboratore. Questo permette di:
- conservarle a lungo nel tempo
- duplicarle
- ricercarle più facilmente
- condividerle istantaneamente con persone remote
- rielaborarle in modo più efficiente
In un contesto nel quale è la rapidità del time to market (o time to delivery nel caso di un prodotto industriale) ad essere uno dei maggiori vantaggi competitivi, poter rielaborare in modo rapido ed efficiente le informazioni legate al prodotto è uno dei punti chiave per mantenere un vantaggio competitivo sostenibile.
Il tipo di digitalizzazione incide molto sulla qualità di rielaborazione. Ad esempio digitalizzare un disegno attraverso una banale “scannerizzazione” o possedere il formato digitale nativo di un sistema CAD, non è equivalente. Dalla qualità del modello informatico dipende, infatti l'efficacia ed il costo della successiva rielaborazione. La differenza in termini di produttività tra l’una e l’altra è di almeno un ordine di grandezza, se non due.
Secondo lo stesso principio, avere un modello bidimensionale o tridimensionale di un prodotto non è equivalente. Come è ormai universalmente accettato, la ricchezza di informazioni di un modello CAD tridimensionale - o per meglio dire la sua intelligenza - è in grado di velocizzare sia lavoro in ufficio tecnico (grazie ad una rappresentazione più vicina alla realtà, alla costruzione automatica di viste bidimensionali ed alla facilità di modifica) che quello dei dipartimenti produttivi (grazie alla fornitura di matematiche precise ed adattabili alle macchine di produzione).
Grazie ai modellatori tridimensionali è già possibile anticipare, validandole in ambito CAD, diverse problematiche tipiche della produzione come ad esempio il controllo delle interferenze tra le parti durante la fase di montaggio oppure la verifica della disponibilità dei componenti in distinta.
La simulazione virtuale rappresenta l’estensione di questo approccio alla ennesima potenza ed ha come obiettivo la verifica funzionale completa del prodotto stesso. Inoltre, abilita una vera propria ottimizzazione dello stesso, sia durante le fasi dello sviluppo prodotto, che come risultato complessivo. Da non sottovalutare la possibilità di automatizzarla quasi completamente, delegando diverse attività ai centri di calcolo o al "cloud computing".
Diventa quindi possibile analizzare, ad esempio, l’adeguatezza della lubrificazione di un ingranaggio, stimare la durata dei cicli di uno stampo, verificare la temperatura di esercizio di un motore elettrico, anticipare i problemi di certificazione di un apparato elettronico, ecc. Tramite la messa a punto di un modello digitale “completo” (prototipo virtuale o digital twin) è possibile anticipare virtualmente (ed a costi accessibili) il funzionamento reale "altrettanto completo" dei prodotti, ed ottimizzarli in funzione degli obiettivi di business.
Simulare a 360°
La SBES (Simulation Based Engineering & Science), altrimenti detta CAE (Computer Aided Engineering) non si può definire una disciplina recente. Esiste ormai da diverse decenni, si insegna in tutte le università tecniche-ingegneristiche e senza di essa non sarebbe stato possibile sviluppare aerei o auto performanti. Partendo da questi settori, sempre più velocemente, si è diffusa a molti altri: oggi non esiste ambito applicativo che non potrebbe beneficiarne.
Questo allargamento di potenzialità è stato oggettivamente favorito da alcuni trend di mercato legato al più generale processo di informatizzazione:
- incremento delle prestazioni hardware, che hanno ridotto i tempi di calcolo
- abbassamento contestuale dei costi hardware
- diffusione della cultura CAE, oggi trattata in tutte le facoltà ingegneristiche
- moltiplicazione di metodologie e strumenti software specifici di una certa disciplina ingegneristica
- semplificazione d'uso degli strumenti di simulazione
- vantaggi economici nel passare dal fisico al digitale per i testi di validazione
Ridotti i costi di ingresso, il CAE risulta oggi accessibile a qualsiasi organizzazione e, all’interno di queste, a più dipartimenti aziendali. Capace di indirizzare opportunità di valore a 360 gradi riguardanti sia la riduzione dei costi, che l'aumento delle prestazioni e della qualità.
E’ possibile oggi simulare contemporaneamente non uno, ma diversi aspetti critici di un prodotto: dalla struttura (FEM) alla fluidodinamica (CFD), all’elettromagnetismo. Si parla in questo caso di Simulazione Multifisica.
E’ possibile simulare i processi produttivi, siano essi basati su componenti plastici, in metallo e/o realizzati con le nuove stampanti additive.
E’ possibile usare il CAE nelle diverse fasi dello sviluppo prodotto perché si adatta ad utilizzatori con competenze diverse. Si parla in questo caso di Simulazione Pervasiva, spesso associata al concetto di Simulazione real-time.
Simulazione Multifisica (e ottimizzazione del prodotto)
L’incremento costante delle funzionalità e delle prestazioni aumenta la complessità dello stesso prodotto a dismisura. Il prodotto diventa un vero e proprio sistema il cui funzionamento finale dipende da un numero estremamente elevato di sotto-componenti e dalla loro interazione.
Analogamente la simulazione per essere efficace deve saper modellare in modo analitico ciascun componente ed il sistema nella sua complessità. Prendendo a riferimento un banale telefono da scrivania, deve essere garantito che la struttura resista a determinati urti, che la pressione di esercizio dei tasti sia adatta alle sensibilità tattili, che il funzionamento dell’elettronica non surriscaldi gli ingombri interni, che le emissioni elettromagnetiche non interferiscano con l’ambiente circostante e che i led siano sufficientemente illuminati ed ovviamente che tutto questo abiliti la funzione principale del telefono, ovvero instaurare una comunicazione di qualità.
Tradizionalmente gli applicativi che si occupano di simulazioni vengono suddivisi in base alle leggi fisiche che stanno alla base della progettazione ingegneristica:
Simulazioni strutturali
Elaborano valutazioni sulla resistenza della struttura del prodotto correlata alla sua funzione. A loro volta si suddividono in analisi strutturali meccaniche statiche o in movimento (multi-body per cinematica e dinamica), acustica e vibrazioni, acustica ambientale, grandi deformazioni e analisi di contatto, dinamica veloce per impatto e crash test.
Simulazioni fluidodinamiche
La fluidodinamica computazionale riguarda lo studio di fenomeni complessi come l’aerodinamica, la termica, i processi multifase di mixing e separazione, reazioni di combustione fino ad arrivare alla determinazione di inquinanti con impatto ambientale, sistemi rotanti e turbomacchine (turbine, pompe, ventilatori).
Simulazioni Elettromagnetiche
Studiano l’effetto della elettricità sul funzionamento dei prodotti, suddivisi tra applicazioni di elettromagnetismo a bassa frequenza (usate per lo studio di motori elettrici e trasformatori) ed elettromagnetismo ad alta frequenza (usato per la progettazione di antenne e di schede elettroniche).
Simulazioni Ottiche
Oggi molto di moda perché oltre al tradizionale supporto alla progettazione di apparati ottici e di illuminazione (lampade, proiettori, guide luce), si occupano del riconoscimento visivo, oggi alla base di evoluzioni tecnologiche di estrema importanza come la realtà virtuale o aumentata e la guida autonoma.
Queste applicazioni devono essere in grado sia di lavorare singolarmente che di interagire tra di loro (si parla in questo caso di simulazione di sistema), perché il comportamento funzionale di un prodotto-sistema, non dipende quasi mai da una singola disciplina fisica. Questo approccio che si chiama appunto multi-fisico, è l’unico in grado nel tempo di garantire l’evoluzione coerente di un modello di simulazione aderente alla realtà e quindi coerente con gli obiettivi dello sviluppo prodotto.
Nell’ambiente integrato di lavoro l’analista ha infatti la possibilità di trovare l'efficienza del sistema, muovendosi appunto nella direzione di ottenere le caratteristiche ideali di prodotto, rispetto al target di mercato.
Sviluppare il prodotto ideale: la simulazione nei processi produttivi
Tradizionalmente l’azienda manifatturiera è divisa in due ambiti ben precisi: progettazione e produzione. Queste funzioni sono spesso contrapposte; infatti, chi progetta non sa esattamente come vengono realizzati i prodotti e d’altra parte un responsabile di produzione non ha competenze progettuali.
Il CAE è stato prima di tutto applicato in fase di progettazione, ma lo stesso approccio può essere applicato per migliorare i processi produttivi, come l’iniezione della plastica, il casting, l’imbutitura e la colata continua. Anche questi sono processi fisici che possono essere digitalizzati per essere validati ed ottimizzati virtualmente.
Un secondo contesto riguarda il Quality Lifecycle Management, molto diffuso in paesi che coniugano grandi produzioni con alta qualità, come la Germania. L’idea di fondo consiste nell’analizzare meglio le tolleranze di un assieme, per abbattere i costi di produzione. Con un approccio statistico (un pezzo prodotto infatti non è mai identico al successivo) è possibile prendere in considerazione eventuali compensazioni per diminuire gli scarti, arrivando a ridurre fino al 5% i costi complessivi di produzione.
In entrambi i casi, la simulazione di produzione può essere integrata a monte nei processi di progettazione e a valle coi processi logistici per ottimizzare il sistema progettuale-logistico-produttivo nel suo complesso.
La simulazione in tempo reale e pervasiva
L’utilizzo ed il posizionamento aziendale del CAE almeno nelle aziende più mature sta cambiando, di pari passo con i requisiti per sviluppare il prodotto ideale.
Storicamente l’introduzione in azienda delle tecnologie CAE è spesso avvenuta al verificarsi di problemi contingenti. Ad esempio: se una azienda sta progettando un grosso impianto e non riesce a raggiungere sperimentalmente gli obiettivi funzionali del progetto attraverso una sperimentazione fisica non ha altre alternative che trasformare il processo in digitale per ottenere dei risultati.
Anche se questo approccio opportunistico ha portato benefici importanti, è necessario partire da un analisi del potenziale, ovvero da una visione complessiva inter-disciplinare ed inter-dipartimentale dell’uso della simulazione. Non sono molte le aziende in grado di impostare una valutazione di questo genere, perché l’esperienza necessaria richiesta è molta, ma questo è l’approccio che produce i migliori risultati nel tempo.
L’implementazione dei sistemi di simulazione non è deve essere un evento sporadico ma un percorso da fare con un partner di fiducia.
La stessa evoluzione degli strumenti CAE favorisce questo approccio. Se, un tempo, l’unico utente della simulazione in azienda era un analista estremamente preparato su determinate applicazioni verticali, oggi esistono metodi e versioni di strumenti semplificati, pensate per altre figure meno specialistiche.
Non si tratta ovviamente di sostituire la profondità della conoscenza di un analista, che resta assolutamente chiave per ottenere prestazioni importanti, ma di affiancarlo con figure diverse ed applicazioni semplificate, per allargarne l’utilizzo aziendale e quindi i benefici.
Un esempio riguarda la fase iniziale dello sviluppo prodotto: il concept. Durante questa prima fase dello sviluppo le alternative sono molte e non possono essere analizzate tutte in dettaglio. A questo livello non è adatta una simulazione profonda e perfetta, che richiede però risorse specializzate e lunghi tempi di calcolo, mentre lo è un approccio semplice con risposte in tempo reale.
Modificare istantaneamente la geometria del concept avendo una sensazione immediata del modificarsi delle variabili multi-fisiche in gioco, anche se come indicazione qualitativa, facilita la realizzazione di un numero più elevato di varianti e quindi una scelta finale migliore.
Ottenere valore dalla simulazione
Le potenziali applicazioni della simulazione abbracciano tutte le discipline ingegneristiche e le loro possibili correlazioni. Da un lato questo è un aspetto positivo perché in teoria tutte le aziende manifatturiere potrebbero trarne un beneficio, applicandola alle proprie attività. Dall’altro lato, le aziende devono saper coniugare le giuste competenze.
È una grande sfida ma che non deve spaventare. Il mondo complessivo della simulazione è molto esteso, ma ogni azienda opera in una nicchia ben precisa di mercato dove sono necessarie specifiche tecnologie.
Per individuare le soluzioni più adatte, trovare un partner diventa un fattore determinante, soprattutto nella fase iniziale di implementazione. Poter contare su una conoscenza estesa specializzata, sia per settore che per ambito verticale rappresenta un grandissimo valore aggiunto.
Ogni azienda rappresenta una realtà a sé: per questo è molto importante poter personalizzare le tecnologie preparando un modello funzionale il più allineato possibile alle necessità di progettazione e sviluppo.
Non è un percorso facile, come del resto non lo sono le sfide dello sviluppo prodotto, ma è una scelta obbligata se si vuole mantenere competitività nel tempo. Per semplificare questo passaggio critico è possibile inizialmente introdurre queste soluzioni in modo graduale, magari partendo da attività di service o consulenza.
Diversi studi hanno già dimostrato un notevole vantaggio prestazionale tra le aziende che hanno introdotto la simulazione nei loro processi e quelle che si affidano ancora a metodi tradizionali. Aberdeen ha pubblicato uno studio nel quale registra una riduzione del costo di produzione nelle aziende che sfruttano la simulazione virtuale fino al 14%, e del tempo di sviluppo fino al 24%.
Sono numeri importanti, che in un mercato sempre più competitivo come quello attuale possono fare la differenza. Se vuoi scoprire le opportunità della simulazione per sviluppare il prodotto ideale e come integrare strumenti avanzati all’interno del processo produttivo, contattaci: uno dei nostri esperti risponderà a tutte le tue domande sull'innovazione di prodotto e di processo.