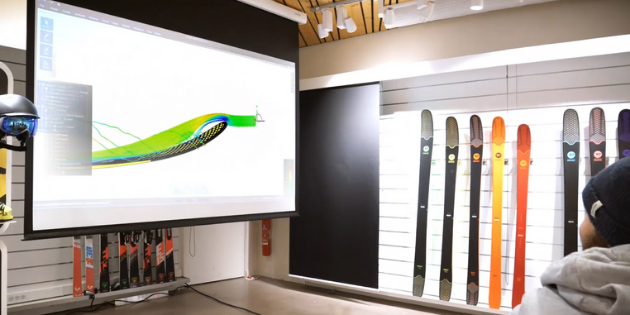
Pubblicato da Alessandro Cinciripini,
Prospettive future della CFD: verso la simulazione in tempo reale
La fluidodinamica computazionale (CFD) è la branca della meccanica dei fluidi che utilizza i metodi di analisi numerica per poter risolvere i problemi di fluidodinamica. I computers vengono utilizzati per svolgere i calcoli richiesti e quindi poter simulare uno svariato numero di condizioni diverse.
Grazie alle simulazioni è possibile indagare a 360° il funzionamento di tutti i componenti e sistemi che lavorano attraverso fluidi: fluidodinamica interna, interazione dei flussi con corpi solidi, meccanismi di scambio termico, aerodinamica esterna, comportamento in transizione di fase eccetera.
In questo articolo vedremo come si è evoluta nel tempo questa disciplina e in quale direzione si sta muovendo.
La CFD inizia la sua storia a partire dagli anni ’60 dove veniva utilizzata principalmente nei campi di ricerca scientifica e nell’aeronautica. Nel corso dei decenni è entrata sempre più a far parte mondo dell’ingegneria, fino ad oggi in cui questo tipo di simulazione è presente in modo capillare nell’industria dei paesi più avanzati.
Il ruolo odierno della fluidodinamica computazionale (CFD) nell’ingegneria
Secondo gli ultimi dati disponibili, il mercato della CFD nel mondo si assesta attorno agli 1.6 miliardi di dollari nel 2018. Solo nel 2012 gli stessi studi riportavano un valore di marcato pari a 750 milioni di dollari. Dati alla mano, a partire dagli anni 2000, la crescita media anno per anno è del 11%, testimoniando come il mondo della simulazione fluidodinamica stia conoscendo un’espansione continua.
I primi soggetti che nello scorso decennio hanno investito nella simulazione fluidodinamica sono stati i gruppi industriali di medie-grandi dimensioni, perchè potevano contare su uffici tecnici più grandi e un maggior capitale da investire. Vennero acquisite figure di analisti CFD, ovvero ingegneri specializzati in fluidodinamica computazionale e con un alto profilo tecnico.
Negli anni più recenti la tendenza è quella di una diffusione delle analisi CFD anche alle realtà medio-piccole: produttori di valvole, componenti di impianto, ventole, scambiatori di calore, componenti elettroniche ecc. Questo processo di “democratizzazione” della simulazione è stato possibile principalmente grazie allo sforzo che stanno compiendo gli sviluppatori dei codici di simulazione in tempo reale per rendere sempre più accessibile questa realtà.
Oggi un numero sempre maggiore di progettisti nelle aziende possono utilizzare applicazioni che non richiedono più sforzi di configurazione numerica e generazione della griglia di calcolo. L’impegno viene concentrato solo nella modellazione dei fenomeni fisici; l’ingegnere, grazie alla simulazione CFD, ha la possibilità di capire a fondo e reinterpretare sotto una luce diversa cosa avviene nei prodotti che sviluppa quotidianamente. Questo permette anche alle piccole e medie imprese di dare un alto valore aggiunto ai propri prodotti, e aumentare competitività sul mercato.
Le aziende che hanno implementato completamente la simulazione in tempo reale CFD nei propri flussi di lavoro utilizzano questo strumento anche per identificare gli scenari operativi in cui si possono verificarsi guasti e rotture, oppure per analizzare le performance e, quando non vengono soddisfatte, studiare soluzioni alternative.
Perché le compagnie introducono la simulazione fluidodinamica negli uffici tecnici
I fattori chiave che guidano la crescita di questo settore sono sostanzialmente due. Il primo riguarda il bisogno crescente di ridurre i costi di sviluppo dei prodotti. Tramite la CFD è possibile snellire il flusso di lavoro dedicato alla progettazione; i costi di sviluppo vengono contenuti grazie alla riduzione al minimo delle prove sperimentali, che si limitano solo alla fase di validazione e certificazione. La riduzione dei costi impatta notevolmente anche sulle azioni di post-vendita e assistenza: al miglioramento delle soluzioni tecniche implementate corrisponde una migliore affidabilità dei prodotti che si traduce in minori costi di manutenzione.
Il secondo fattore riguarda i tempi di sviluppo: diminuire il time-to-market è diventato un dogma in tutti i soggetti che operano nel settore industriale, ed è l’unico modo per poter competere sul mercato attuale. Le aziende devono essere molto più dinamiche che in passato per riuscire a stare al passo con le evoluzioni della domanda e al tempo stesso continuare a fornire soluzioni flessibili per i diversi mercati a cui si rivolgono. Il miglior modo per ottimizzare le prestazioni senza impattare ulteriormente sui tempi e i costi di sviluppo è quello di introdurre le simulazioni nella fase iniziale di concept dello sviluppo di prodotto.
Il futuro della simulazione CFD
La simulazione CFD si basa sulla definizione di modelli fisici e un determinato numero di parametri in ingresso che possono variare entro certi limiti (vincoli) definiti dal tecnico. Gli ambienti di simulazione più sofisticati sfruttano tecniche Design of Experiments (DoE) per ricercare in modo intelligente i punti di funzionamento di ottimo, con l’obiettivo di minimizzare il numero di run e i tempi di calcolo. Questo approccio dà degli ottimi risultati ma occorrono comunque decine o centinaia di lanci in base al numero di variazioni permesse ai parametri, per mappare efficacemente la sensitività del modello. I tempi richiesti per il calcolo possono essere molto alti, o perlomeno non compatibili con i tempi aziendali.
Oggi si stanno cercando di superare questi limiti con approcci alternativi per esplorare in modo “intelligente” tutto il range costruttivo permesso. Due strade differenti possibili sono:
Metodo aggiunto (adjoint method).
L’approccio cosiddetto ‘aggiunto’, fa parte della tipologia di algoritmi di ottimizzazione gradient-based. Esso rappresenta un’alternativa interessante allo studio DoE: l’algoritmo permette di identificare come deformare la geometria per ottenere variazioni nel parametro definito come funzione obiettivo. Matematicamente calcola i gradienti della funzione da ottimizzare e il costo computazionale è quello di un secondo calcolo CFD sullo stesso modello.
Questo approccio è molto potente, ma è adatto solo a quelle casistiche in cui la configurazione da studiare è già vicina a quella di ottimo, mentre invece dà scarsi risultati se si ha un’idea meno chiara di come strutturare il design. Il limite è dato dal fatto che la soluzione sarà un punto di ottimo locale, che non per forza corrisponde all’ottimo globale.
Simulazione in tempo reale.
Nata da pochissimi anni, la simulazione real-time è estremamente innovativa e sta rivoluzionando il mondo della CFD. Questi software permettono di eseguire analisi in tempo reale, rese possibili grazie agli enormi sviluppi compiuti in questi anni nel mondo dell’hardware per la computer grafica destinato al gaming. Sono state sviluppate delle schede grafiche così avanzate da avere capacità di calcolo in parallelo di gran lunga superiori a quelle di un microprocessore.
Grazie alla velocità con cui si ottengono i risultati è possibile eseguire una parametrizzazione globale di tutto il modello, analizzando in pochi minuti tutte le permutazioni delle configurazioni definite. I limiti dell’approccio riguardano il modello fisica, che non può spingersi oltre una certa complessità e il livello di dettaglio raggiungibile.
La simulazione CFD in tempo reale
Gli ingegneri fluidodinamici che svolgono analisi CFD da anni, hanno accolto con diffidenza questi applicativi, perché sembra inverosimile poter ottenere risultati fluidodinamici in tempi così brevi. L’utente di un software di simulazione in tempo reale non vede tutte le scelte di modellazione abituali come ad esempio: scelta del modello di turbolenza, infittimento della griglia di calcolo o modelli di scambio termico. La simulazione viene impostata in modo totalmente automatico, perché tutte le scelte di modellazione sono state fatte a monte dagli sviluppatori. La discretizzazione delle geometrie avviene non attraverso la definizione della classica griglia di calcolo, ma tramite i voxels, ovvero una griglia cartesiana che scompone i corpi in mattoni elementari. Le equazioni vengono poi risolte all’interno di essi.
In tempi recenti sono stati compiuti diversi studi per capire le potenzialità di questi strumenti, ma soprattutto avere una stima precisa dello scarto tra i risultati ottenuti nelle simulazioni real-time rispetto a simulazioni CFD di dettaglio. Sono stati presi a campione diversi problemi fluidodinamici a cui vengono applicate le stesse condizioni operative. In alcuni casi i risultati sono stati sorprendenti.
Il risultato relativo alla portata smaltita in una valvola a globo, interessata da un salto di pressione imposto, si discosta del 6% rispetto allo stesso risultato ottenuto con una simulazione CFD standard.
Per la simulazione CFD standard si è dovuto pre-processare il CAD di partenza per semplificarlo e ricavare il volume fluido, è stata costruita la griglia di calcolo e sono stati impostati i modelli fisici. Infine il calcolo è durato circa 1 ora.
L’analisi col solutore real-time è stata svolta nel giro di qualche minuto, in quanto non è necessario né semplificare il CAD, né creare la griglia di calcolo, e infine la simulazione transitoria va a convergenza in qualche secondo.
In un altro test, è stato comparato il risultato di prevalenza richiesta a una ventola di raffreddamento per vincere le perdite di carico di un case contenente PCB e componentistica elettronica. Qui lo scarto è stato ancora minore ovvero pari al 4%.
È stato analizzato anche un problema di aerodinamica esterna su un TIR in movimento investito da aria ferma. Rispetto all’analisi CFD standard il coefficiente di resistenza (drag) si discosta del 9%.
Un limite di questa tecnologia che è emerso riguarda i gas in regime comprimibile, ovvero alle alte velocità (ugelli e altri componenti operanti in regime transonico). In questi casi il risultato può discostarsi in modo considerevole perché il solutore non considera gli effetti di comprimibilità del fluido.
Tenuto conto delle lievi differenze dei valori di output delle analisi, il dato impressionante è che tutte queste simulazioni sono state portate a termine nel giro di pochissimi minuti, proprio perché è possibile importare direttamente il CAD nativo, impostare le condizioni al contorno ed avere subito il risultato. Il software, che è inserito in un ambiente CAD, dà la possibilità di fare modifiche geometriche e vedere all’istante come cambiano i risultati sui monitor definiti dall’utente. In questo modo si possono impostare velocemente esplorazioni parametriche in ottica DoE.
I trend futuri dell’analisi CFD stanno guardando verso la simulazione parametrica come strumento per indagare un ampio spettro di configurazioni possibili in modo automatico.
In questo quadro i software di simulazione CFD in tempo reale offrono un valido strumento a supporto della progettazione. Questi non sostituiscono le simulazioni CFD tradizionali effettuate dagli ingegneri analisti, ma le affiancano. L’analista verifica un numero minore di configurazioni, perché già scremate dal progettista, può focalizzare l’attività sull’ottimizzazione del prodotto. La riduzione delle iterazioni tra analista e progettista, migliora il flusso di lavoro dell’ufficio tecnico in generale, riduce il time-to-market e i costi di sviluppo.
L’utilizzo di strumenti di simulazione CFD real-time ha un impatto positivo anche per le progettazioni dove è richiesto un livello di ottimizzazione ridotto, ovvero quegli scenari in cui nel funzionamento reale possono intervenire altri elementi che è impossibile governare in fase di progettazione. In questi casi in cui è complesso fare una modellazione CFD efficace, la simulazione real-time è l’unica strada percorribile perché dà una risposta veloce ed economica.
Scopri come integrare un software di simulazione CFD all'interno del processo di progettazione e di produzione della tua azienda. Contattaci, uno dei nostri esperti risponderà a tutte le tue domande.