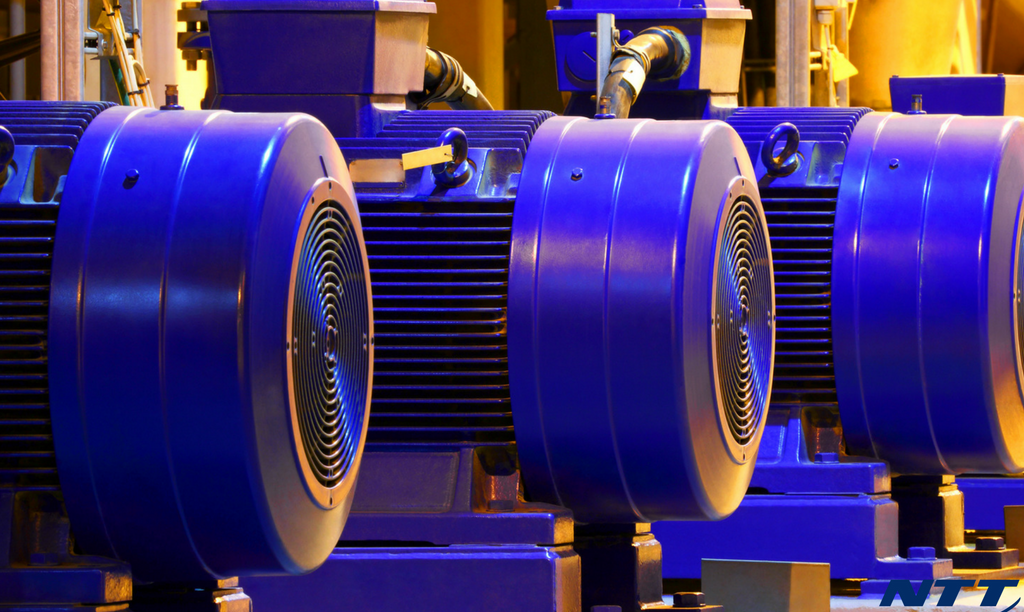
Per predire in maniera accurata le prestazioni di una macchina di questo tipo è necessario spesso considerare sia la temperatura raggiunta durante il regolare esercizio che la storia di carico a cui sono stati sottoposti i singoli componenti della macchina elettrica. I modelli e le tecnologie seguenti possono essere implementate per una simulazione avanzata e di dettaglio del motore elettrico:
- Isteresi vettoriale
- Demagnetizzazione dei magneti permanenti funzione della temperatura
- Calcolo accurato delle perdite di potenza nei pacchi di lamierini magnetici
- Magnetostrizione
Ad esempio Il processo necessario alla produzione dei lamierini può variare le proprietà magnetiche del prodotto finale. Nello specifico le moderne procedure di taglio laser delle lamiere magnetiche comportano una modifica della microstruttura del materiale nella zona di taglio, a cui consegue un aumento locale delle perdite di potenza per isteresi magnetica durante il funzionamento della macchina.
![]() |
Calcolo delle perdite nel nucleo (coreloss) di un motore sincrono a magneti permanenti |
L'efficienza cambia in base alla velocità di rotazione ed al carico; pertanto, nella progettazione del motore e dei controlli, si utilizza spesso la mappa di efficienza della macchina su un piano coppia-velocità come indice delle prestazioni sull’intero range di funzionamento.
I più avanzati strumenti di simulazione eseguono in maniera automatica il calcolo della mappa di efficienza e le caratteristiche coppia-velocità di un motore a magneti permanenti, utilizzando strumenti dedicati di visualizzazione dei risultati, in modo che il comportamento della macchina possa essere compreso e valutato facilmente ed in tempi rapidi.
![]() |
Mappa di efficienza di un motore sincrono a magneti permanenti interni (IPM) |
L’importanza della simulazione multi-fisica e delle tecniche di ottimizzazione
Progettare un motore elettrico ad alte prestazioni non è una cosa semplice. Oltre ai principali vincoli tecnici (costo, ingombri del motore, caratteristiche del circuito di raffreddamento, specifiche dell'inverter), i requisiti richiesti dal cliente per le diverse tipologie di motore si estendono a diversi domini afferenti a fisiche diverse:
- Termodinamica: portata e temperatura del refrigerante, temperature ambientali, nonché le temperature a cui sono sottoposti gli avvolgimenti ed i magneti permanenti.
- Meccanica strutturale: ingombri, potenza meccanica del motore, tolleranze di lavorazione, forzanti sui cuscinetti, vibrazioni, ecc.
- Elettrotecnica: tensione e correnti, proprietà specifiche dell'inverter, ecc.
- Acustica: Propagazione di un’onda di pressione acustica, su un certo dominio di calcolo, indotta dalle vibrazioni del motore elettrico
Per ottimizzare la macchina elettrica oggetto della progettazione, la simulazione deve considerare tutti i parametri afferenti alle diverse fisiche contemporaneamente, in modo da conseguire una reale ottimizzazione multi-obiettivo, che consideri cioè le performance della macchina nei diversi domini di analisi descritti precedentemente, per trovare l’ottimo, e cioè il miglior compromesso fra obiettivi fra loro contrastanti.
In questo ambito non è più possibile sviluppare i singoli componenti in maniera "classica", in cui ciascun componente, con le proprie specifiche, viene progettato separatamente e poi assemblato successivamente. Piuttosto è necessario sviluppare un workflow di progettazione che incorpori la simulazione per tenere conto delle interazioni dinamiche tra i componenti, nonché di tutti i parametri necessari per determinare soluzioni ottimali e garantire la solidità del progetto.
![]() |
Workflow di simulazione multifisica di un motore elettrico |
Analisi del sistema
La creazione di un motore ottimale per veicoli ibridi ed elettrici richiede che più componenti elettronici e meccanici siano progettati e testati insieme come un sistema. Identificare e scegliere quale sia il miglior compromesso durante la fase di progettazione è difficile, ma attraverso strumenti di simulazione che implementino sia tecniche per l’analisi multi-fisica e muilti-dominio che strategie di ottimizzazione questo obiettivo è realizzabile.
Convenzionalmente, la progettazione dell’apparecchiatura di controllo (inverter) e quella elettromeccanica del motore adottano processi indipendenti l’uno dall’altro, cosicché è difficile coordinare la progettazione mirando all'ottimizzazione dell'intero sistema.
Tuttavia, la modellazione virtuale dell’intero sistema, può essere implementata da un'analisi che accoppia uno strumento di analisi di campo elettromagnetico con un simulatore di sistema circuitale e dei controlli.
Esistono due principali metodologie che collegano un'analisi di campo elettromagnetico con l'analisi circuitale e di sistema: la co-simulazione, che esegue nel transitorio un accoppiamento diretto fra modello FEM e simulatore circuitale, e una simulazione di sistema che si basi su un modello a parametri concentrati (Reduced Order Model) generato a partire dalle simulazioni FEM del singolo componente.
Strumenti di simulazione avanzati possono gestire entrambe le metodologie descritte in risposta alle diverse esigenze di simulazione.
![]() |
La simulazione di sistema: al centro il modello del motore elettrico |
Il livello di dettaglio conseguibile con una co-simulazione è maggiore di quello ottenibile da una simulazione di sistema che incorpori un modello a parametri concentrati. Difatti la precisione e la quantità di output ottenibili nel primo caso è pari a quella raggiungibile con la sola simulazione FEM. Di contro la simulazione di sistema che implementi modelli di ordine ridotto è molto più veloce e consente di implementare controlli ad altissima velocità.
Scopri come integrare un software di simulazione all'interno del processo di progettazione e di produzione della tua azienda. Contattaci, uno dei nostri esperti risponderà a tutte le tue domande.